A conversation with Envirotech’s Andy Delisi
Six years ago, Andy Delisi was looking for a role at a business that strived to be innovative, do good for the planet, and get people excited about sustainability. He found that opportunity as a Business Development Manager at Envirotech. Based in Ontario, Canada, the company works with enterprise-level organizations to remanufacture pre-owned furniture, fixtures and equipment (FF&E) and reintroduce them to commercial markets across North America.
When Andy met Rheaply’s Chief Impact Officer Garr Punnett, it felt like they were “speaking the same language” from their very first meeting. It was clear both organizations shared aspirations for bringing the circular economy to life. The companies began working together with a warehouse cleanout for a large tech company, which has since grown into a thriving partnership.
Andy currently facilitates Envirotech’s partnership with Rheaply to help clients refurbish their workplaces’ FF&E that are then exchanged on the Rheaply platform. There’s much that Andy is excited about for the Rheaply and Envirotech partnership. With every conversation between Rheaply and Envirotech, “We learn something new about how we can develop both of our innovative platforms to take things to the next level.”
Rheaply talked with Andy to learn how companies can become their own original equipment manufacturers (OEM) to furnish their workplaces with high-quality FF&E at competitive prices—all while keeping materials circulated and out of the landfill.
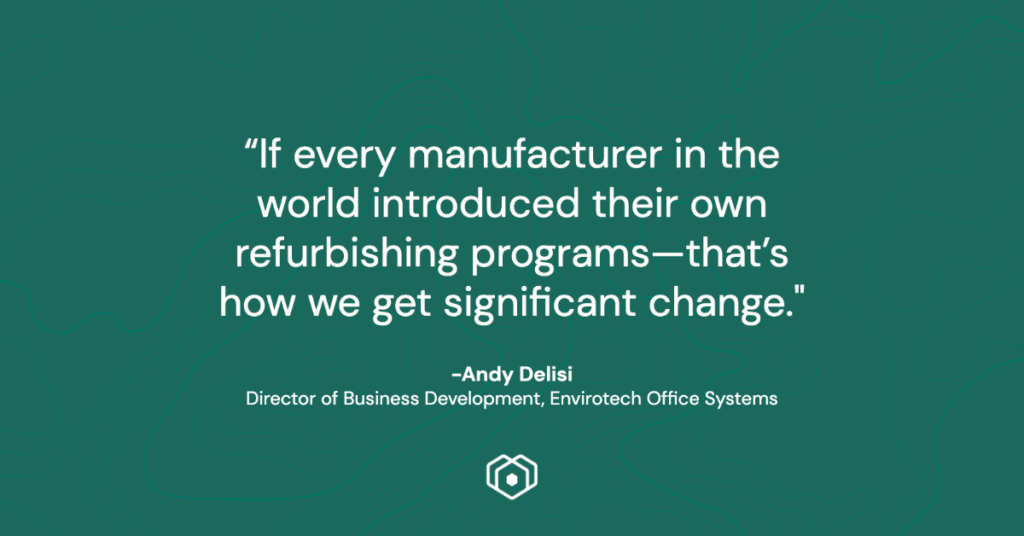
The fast furniture problem today
Fast-furniture is an indisputable problem at the individual level; our world is addicted to cheap products that are not built to last and use materials that make repairs almost impossible. But Andy is quick to point out that “the everyday person also works for organizations that are throwing out millions of tons of fast-furniture every year” because they face too many obstacles when trying to rehome unwanted FF&E.
There is a pervasive stigma around remanufacturing, reuse and refurbishing that conjures images of unsightly ‘used’ products for consumers. Built environment professionals for commercial spaces might avoid using secondhand products out of fear that they will reflect poorly on the image of Fortune 100 or 500 companies.
Even organizations that are committed to rehoming used FF&E encounter logistical hurdles. According to Andy, the “biggest pain points come down to planning and making it as easy as possible to understand what your options are.” When an organization owns lots of assets across buildings, locations, and campuses, they are often not redeployed or used in the most effective way possible. Outdated spreadsheets and floor plans are passed along from one facilities manager to the next, making reuse within an organization complicated, inefficient, and time-consuming.
Companies such as retailers and tech companies often use FF&E that is custom-made to their workplaces. But the cost of decommissioning used FF&E can be daunting, especially if it is not easily outfitted to other spaces.
Andy personally isn’t against solutions like recycling or carbon offsets, but points out that they aren’t effective long-term solutions. “It’s really understanding that the problem is happening and diversion from landfill once is not true circularity – it’s about materials being put to full and active use for the duration of their lifespans.”
What is an OEM?
OEM stands for original equipment manufacturer. This refers to an organization that makes equipment from parts sourced from other organizations.
The furniture opportunity
As a company that helps clients with facility move outs, Envirotech has seen firsthand how “everyone is rethinking space right now—planners are even thinking two to three years ahead of how to move out of an office space.”
Companies that rely on specialized FF&E for their workspaces can become their own OEM to have more control over their supply chain. By salvaging products that would typically be going to landfills and repurposing them, companies also have greater quality control and reduced costs. This also helps significantly lower organizations’ carbon footprints by mitigating the negative environmental impacts that the extraction of both raw and recycled materials has on our ecosystems.
Outsourcing that production to an OEM can be cheaper, especially at scale. An OEM model is more cost-effective for startups and smaller companies that don’t have their own established production lines either domestically or abroad. Manufacturers still keep all trademarks and intellectual property rights of your designs and products.
Relying on third party OEMs does have drawbacks. It can take time and effort to find reliable suppliers of OEM, which might also require guaranteed volumes of custom product order.
Envirotech’s role
Envirotech is an example of an organization that functions as its own OEM. By having in-house expertise to repair and refurbish used FF&E, and the ability to source parts from its own inventory, Envirotech is able to recirculate goods without solely having to rely on outside vendors.
Traditional manufacturers are constantly innovating and redesigning their furniture so they can sell you the latest and greatest from their product lines. Envirotech and its partners have a vested interest in keeping up with trends and innovating with already-extracted materials. Refurbishment prevents having to add new products and materials into circulation, and gives FF&E new life. Once partners of Envirotech see the quality of restored and reupholstered products firsthand, they realize it’s “a no-brainer” when looking for high-end furniture at bargain prices, including brands like Herman Miller.
Envirotech fills in logistical gaps for companies that they might not even know exist. They provide high-touch support that is crucial to ensuring all aspects of a move-out and furniture tack-back process run smoothly. They perform a site evaluation, collect detailed inventory data, take lots of asset photos, and enter all that manually into a database. Planning ahead is essential to rehoming as many items, and Envirotech’s options become more limited when brought on last-minute to a project.
How to introduce remanufacturing and reuse in your own organization
If you want to introduce reuse at your own organization, make it easy for stakeholders to understand the different options and benefits of reuse for built environment professionals and consumers alike. Many organizations are coming from the perspective of reducing carbon emissions and zero waste goals, but “the other big component is really the economic impact and cost savings that come from effective remanufacturing and reuse.” The majority of organizations come to Envirotech because they want high-end furniture without the high-end price—who wouldn’t want to save 30% on all furniture buildouts without losing quality and helping the environment?
“A comprehensive analysis of an organization’s furniture assets is the first step towards becoming your own OEM,” says Andy. “Understanding exactly what can be reused, remanufactured and repurposed will give organizations a new, sustainable outlook on furnishing office space and renovating existing buildings.” Often the problems that can be solved by reuse are “hiding in plain sight,” such as inventory sitting in warehouses or equipment gathering dust in utility closets.
We also need to disincentivize throwing away reusable items by incrementally incorporating reused materials. Tenders are one example that Andy cites as an effective policy for driving circularity at the municipal level, and sees this approach extending into company policies as well. If every organization required projects to contain a certain percentage of reused materials, the demand for circular solutions would increase.
Planning in advance has ripple benefits across your projects and organization. If the timing is right, the resale value of goods can outweigh the cost of decommissioning FF&E.
With Rheaply you can know where assets are and then work with partners like Envirotech to plan your options months or even years in advance, extending the time and amplifying the values saved.
Rheaply and Envirotech: growing together
Envirotech envisions a future where circularity reduces the amount of extracted materials required to make new furniture by innovating and redesigning existing products that can be remanufactured. Envirotech’s long-term client partnerships are key to its ability to remanufacture and rebuild FF&E to use for generations to come. Rheaply provides the exchange platform where this exchange and collaboration can flourish.
Andy sees a number of impacts from the Envirotech and Rheaply systems coming together.
Envirotech and Rheaply both recognized a need for places where reuse can happen, both virtually and in the workspace. The Rheaply platform’s enhanced planning abilities make it easier to be proactive in working together to regenerate significantly more value. Users can know when a product will be decommissioned and will be available, which extends the timeframe for redistributing items and increases the chances of that inventory going to market. Asset tracking helps organizations further understand the scale of the reuse problem so that they can shift to a lasting solutions.
Now when Envirotech employees like Andy start a new project, they use Rheaply to collect data and catalog inventory to immediately know immediately what’s available without having to physically go out to sites. Andy enthused that “every day we look at how Rheaply’s product makes the efficiency and accuracy part of the equation of understanding assets so much easier and … so much more proactive that working together we can reclaim and regenerate significantly more value than we could have done alone.”
But Andy’s most important takeaway is that “together we can make a significant impact,” not just with Rheaply and Envirotech, but all organizations working in the circular economy. “If every manufacturer in the world introduced their own refurbishing programs—that’s how we get significant change.”