Rheaply is excited to launch a brand new guest blog series! We’re inviting contributors from the world of sustainability and circularity to share their thoughts, opinions, and hopes for the future of the industry.
This article comes from our friends Jack Rusk, Director of Climate Strategy, EHDD and Erin Woodward, EHDD.
Last month, the U.S. Green Building Council (USGBC) released the draft language for the newest version of the LEED standard for existing buildings—aligning their industry-leading certification with rapidly evolving consensus on the urgency to address social equity and climate change on every project. “LEED v5,” explains the USGBC, “provides simple, clear steps for delivering ultra-low-carbon buildings” while requiring “social impact assessment” as a prerequisite for certification.
Notably, the standard also includes credits for reducing embodied carbon during renovations. This reflects the reality that, once best efforts have been made to reduce energy-related emissions, the largest remaining source of emissions are those “embodied” in materials as a result of their extraction, manufacturing, and transportation. This much has, across much of the industry, become obvious. What might surprise some designers, however, is that the LEED credit titled “Embodied Carbon of Interior Materials during Renovations” makes no mention of procuring lower-carbon materials.
Instead, LEED v5’s embodied carbon reduction strategies are wholly focused on reuse and circularity. This may appear out of sync with decades of leadership from LEED insisting that manufacturers be transparent about their products’ environmental impacts. This dramatic reframe challenges the notion that we can address climate impacts with low-carbon products alone.
It is no longer enough to acquire the lowest carbon products. It’s time to ask ourselves if new products are needed at all.
Interiors, embodied carbon, and circularity
The shift to circularity can be contextualized within an emerging challenge: the growing impact of interiors on a building’s overall embodied carbon emissions. Currently, embodied carbon reductions are typically focused on the building’s core and shell, which account for a significant portion of embodied carbon. However, as we make strides in reducing emissions from structure and envelope, the embodied carbon from interiors contributes a larger overall proportion of a building’s emissions—especially considering the churn of interior materials over the lifetime of a building. This trend is more pronounced in retrofit projects, where the emissions savings from reusing a building’s core and shell make interiors (and building systems) the preponderance of a project’s total carbon emissions.
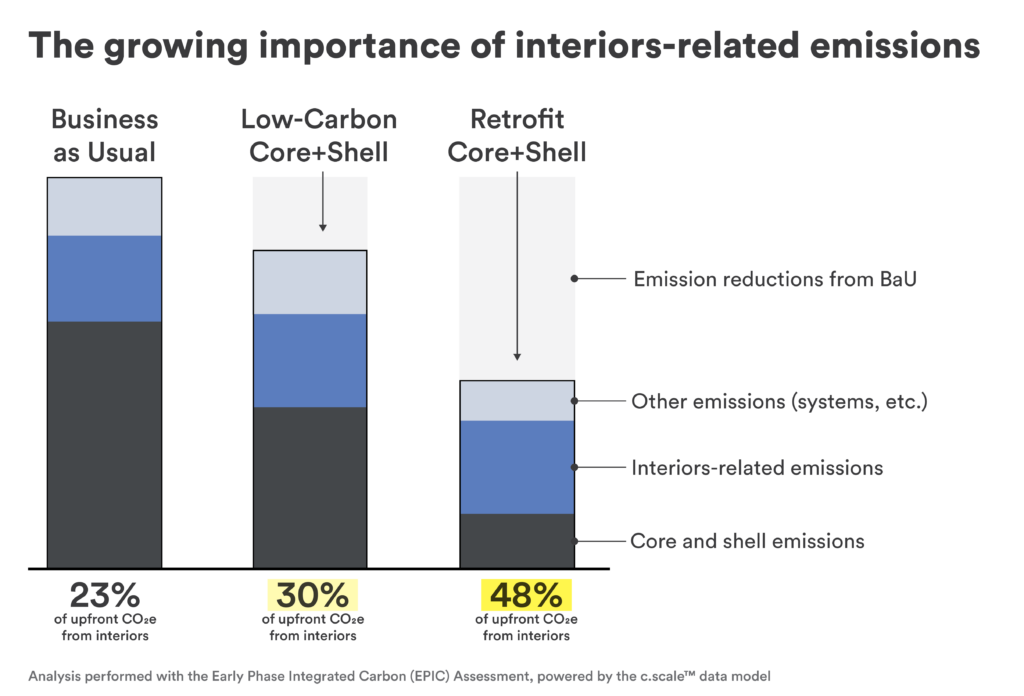
In an analysis performed with EHDD’s Early Phase Integrated Carbon (EPIC), powered by the c.scale™ data model, interiors-related emissions could soon account for 48% of a building’s embodied carbon emissions.
Graphic courtesy of EHDD.
Simply relying on low-carbon procurement strategies is not enough to address these emissions. To tackle this effectively, we must adopt a holistic approach that foregrounds circularity. The industry has grown comfortable with the truism that “the greenest building is the one that’s already built;” to decarbonize our built environment, we need to adopt similar thinking at smaller (and larger) scales. In our approach to interiors, we might say that “the greenest product is the one that’s already manufactured.”
A “yes, and” approach to low-carbon design
Where procuring lower-carbon products allows us to incrementally reduce emissions, reuse and circularity moves us from marginal to transformative reductions in a project’s carbon footprint. This doesn’t mean we should undervalue or ignore the procurement of low-carbon materials. The role of EPDs (and the foundational work of tools like EC3 which make them accessible) remains vital. Not every project will offer the possibility of material reuse and, even on projects where reuse is a first priority, some procurement of new materials is likely unavoidable. Rather than a dichotomy between reuse and low-carbon procurement, we need both—maximizing circularity everywhere we can, then procuring low-carbon materials everywhere we cannot.
EHDD used this “yes, and” strategy in our approach to our renewal and renovation of the American Institute of Architects (AIA) Headquarters in Washington, D.C. When considering each aspect of that project, we used circularity strategies to first “use less” and then, where we had to procure new materials, focused on how to “use better” by reviewing EPDs, HPDs, and the like.
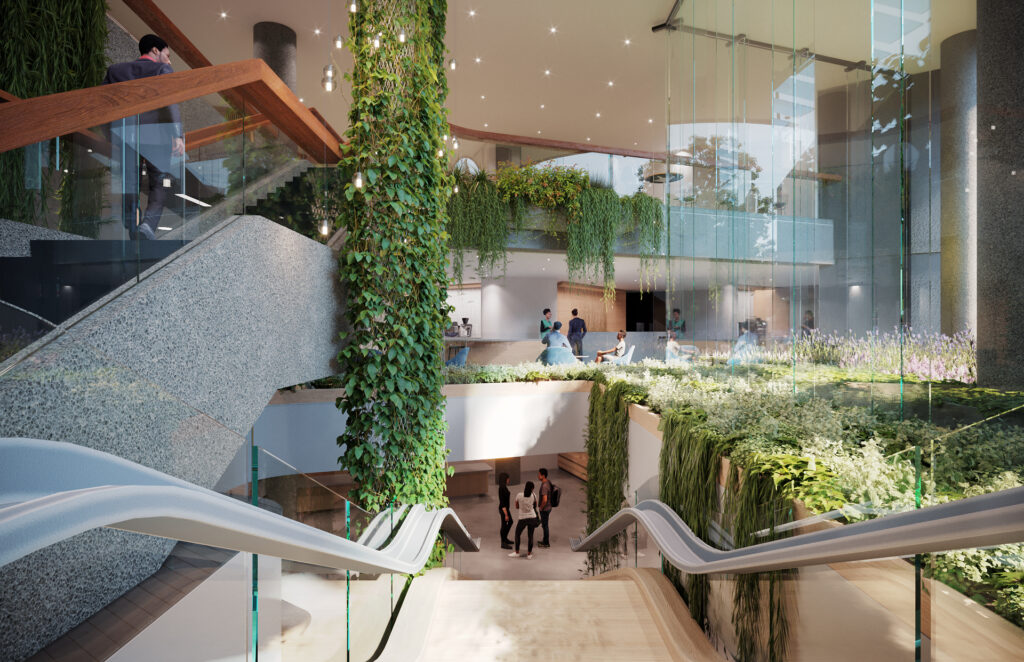
The AIA Headquarters renewal set forward an ambitious whole life carbon target, and met it through a combination of design, circularity, and procurement strategies. You can read more about the project in the RMI and USGBC report Driving Action on Embodied Carbon in Buildings.
Graphic courtesy of EHDD.
For example – EHDD’s design extended an existing, two-story atrium to a lower level. Rather than rebuilding the entire atrium stairway, we chose to keep and refurbish the historic stair, a key feature of the original 1973 design. Where a new stair was needed to extend access to the lower level, we selected low-carbon timber. And through a systematic process of sorting, grading, and refurbishing, the team was able to reuse nearly 90% of the building’s legacy furniture.
For the AIA, circularity was about more than just reducing carbon emissions. It was about preserving and recontextualizing the organization’s history—letting the existing building and finishes tell new stories as the AIA works to make good on its commitment to an equitable and decarbonized built environment. The renovation of their headquarters is one such project, and LEED v5 is a mechanism for creating many more.
Digitizing reuse for LEED v5
We’ve explored the rationale behind USGBC’s unwavering commitment to carbon reduction through reuse and circularity with LEED v5. Having delved into the ‘why,’ it’s imperative to address the ‘how.’
While digital marketplaces like Facebook excel at small-scale, peer-to-peer reuse, architects and interior designers seeking specific, high-quality used materials, consider it essentially a non-starter. Unless you have hours set aside for roaming through your local building materials reuse center, you may not have any promising methods to source reusable materials for your project today. Rheaply offers a new, alternative resource for purchasing high-quality used materials for architecture and design projects.